ໃນໂລກຂອງການຜະລິດໂລຫະ, ຄວາມແມ່ນຍໍາແມ່ນສໍາຄັນ. ບໍ່ວ່າຈະເປັນເຄື່ອງຈັກອຸດສາຫະກໍາ, ການອອກແບບສະຖາປັດຕະຍະກໍາ, ຫຼືວຽກງານສິລະປະທີ່ສັບສົນ, ຄວາມສາມາດໃນການຕັດໂລຫະແຜ່ນຢ່າງຖືກຕ້ອງແລະລະອຽດແມ່ນມີຄວາມຈໍາເປັນ. ໃນຂະນະທີ່ວິທີການຕັດໂລຫະແບບດັ້ງເດີມມີຄວາມໄດ້ປຽບຂອງເຂົາເຈົ້າ, ການມາເຖິງຂອງເຕັກໂນໂລຊີ laser ໄດ້ປະຕິວັດອຸດສາຫະກໍາ, ສະຫນອງຄວາມແມ່ນຍໍາແລະປະສິດທິພາບທີ່ບໍ່ສາມາດແຂ່ງຂັນໄດ້. ໃນ blog ນີ້, ພວກເຮົາຈະເຈາະເລິກເຂົ້າໄປໃນສິລະປະຂອງການຕັດໂລຫະທີ່ມີຄວາມແມ່ນຍໍາ, ໂດຍເນັ້ນໃສ່ໂດຍສະເພາະກັບເຕັກໂນໂລຢີນະວັດກໍາຂອງ.laser ຕັດໂລຫະ.
ຕັດໂລຫະແຜ່ນໄດ້ເປັນຂະບວນການພື້ນຖານໃນການເຮັດວຽກໂລຫະສໍາລັບສັດຕະວັດແລ້ວ. ຈາກເຄື່ອງມືມືແລະເຄື່ອງຕັດກັບເຄື່ອງຈັກທີ່ກ້າວຫນ້າ, ການພັດທະນາເຕັກໂນໂລຢີການຕັດໂລຫະໄດ້ຖືກຂັບເຄື່ອນໂດຍການສະແຫວງຫາຄວາມແມ່ນຍໍາແລະປະສິດທິພາບຫຼາຍກວ່າເກົ່າ. ວິທີການແບບດັ້ງເດີມເຊັ່ນການຕັດ plasma ແລະການຕັດ waterjet ໄດ້ຖືກນໍາໃຊ້ມາດົນນານສໍາລັບຄວາມສາມາດໃນການສ້າງຮູບຮ່າງແລະການຈັດການໂລຫະ, ແຕ່ພວກມັນມັກຈະມີຂໍ້ຈໍາກັດກ່ຽວກັບຄວາມສັບສົນແລະຄວາມແມ່ນຍໍາ.
ເຂົ້າສູ່ການຕັດດ້ວຍເລເຊີ, ເທັກໂນໂລຍີການປ່ຽນແປງເກມທີ່ກໍານົດສິ່ງທີ່ເປັນໄປໄດ້ໃນການຜະລິດໂລຫະແຜ່ນ. ໂດຍການນໍາໃຊ້ພະລັງງານຂອງລໍາແສງເລເຊີທີ່ສຸມໃສ່, ວິທີການຕັດແຂບນີ້ສາມາດຕັດໂລຫະປະເພດຕ່າງໆທີ່ມີຄວາມແມ່ນຍໍາແລະຄວາມຊັບຊ້ອນດ້ວຍຄວາມແມ່ນຍໍາທີ່ບໍ່ກົງກັນ. ຂະບວນການດັ່ງກ່າວກ່ຽວຂ້ອງກັບການນໍາແສງເລເຊີທີ່ມີພະລັງງານສູງໄປຫາພື້ນຜິວໂລຫະ, ການລະລາຍ, ການເຜົາໄຫມ້, ຫຼືການລະເຫີຍຂອງວັດສະດຸເພື່ອສ້າງການຕັດທີ່ສະອາດ, ຊັດເຈນກັບພື້ນທີ່ທີ່ໄດ້ຮັບຜົນກະທົບຈາກຄວາມຮ້ອນຫນ້ອຍທີ່ສຸດ.
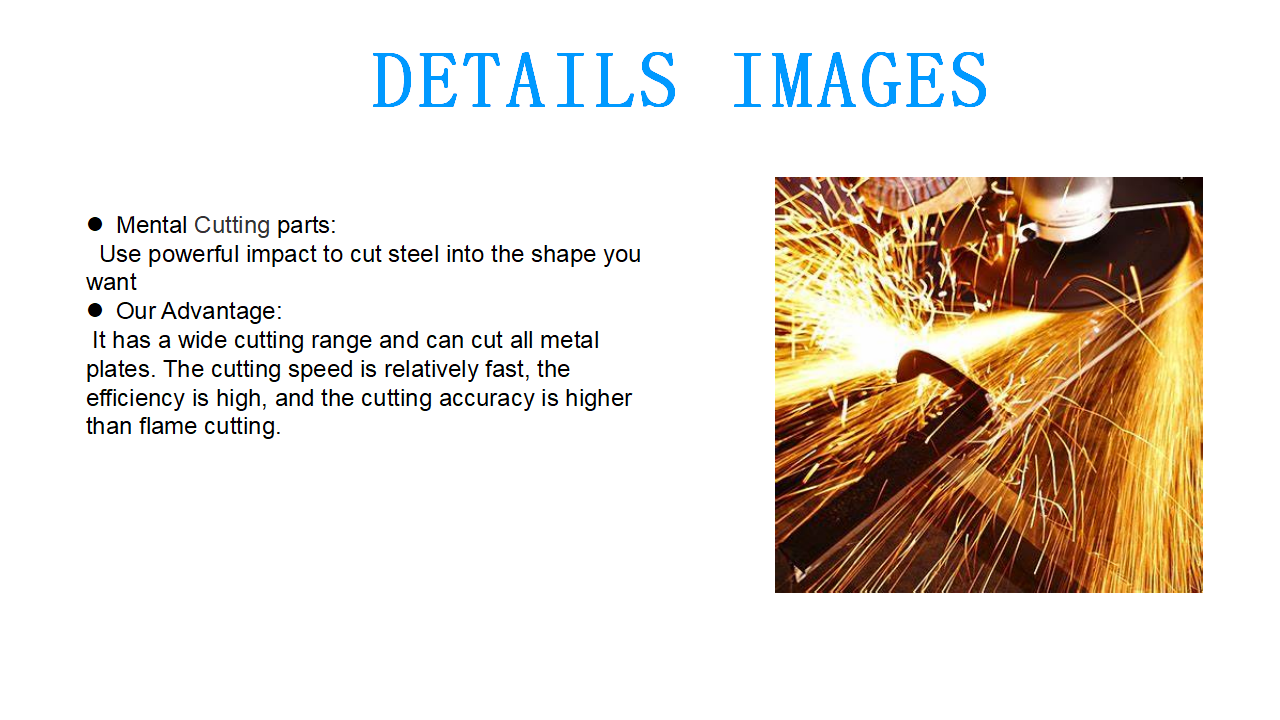
ຫນຶ່ງໃນຂໍ້ໄດ້ປຽບທີ່ສໍາຄັນຂອງຕັດໂລຫະແມ່ນຄວາມສາມາດຂອງຕົນໃນການຜະລິດການອອກແບບ intricate ແລະຮູບຮ່າງສະລັບສັບຊ້ອນທີ່ມີຄວາມແມ່ນຍໍາພິເສດ. ບໍ່ວ່າຈະເປັນຮູບແບບ intricate ສໍາລັບໂລຫະຕົກແຕ່ງຫຼືອົງປະກອບທີ່ຊັດເຈນສໍາລັບເຄື່ອງຈັກອຸດສາຫະກໍາ, ການຕັດ laser ສະຫນອງລະດັບຂອງລາຍລະອຽດແລະຄວາມຖືກຕ້ອງທີ່ບໍ່ມີໃຜທຽບກັບວິທີການຕັດແບບດັ້ງເດີມ. ລະດັບຄວາມແມ່ນຍໍານີ້ແມ່ນມີຄຸນຄ່າໂດຍສະເພາະໃນອຸດສາຫະກໍາທີ່ຄວາມທົນທານທີ່ແຫນ້ນຫນາແລະຂໍ້ກໍານົດທີ່ແນ່ນອນແມ່ນບໍ່ສາມາດຕໍ່ລອງໄດ້.
ຍິ່ງໄປກວ່ານັ້ນ, ການຕັດດ້ວຍເລເຊີແມ່ນຂະບວນການທີ່ມີປະສິດທິພາບສູງທີ່ຫຼຸດຜ່ອນສິ່ງເສດເຫຼືອຂອງວັດສະດຸແລະຫຼຸດຜ່ອນຄວາມຕ້ອງການສໍາລັບການສໍາເລັດຮູບຂັ້ນສອງ. ຄວາມແມ່ນຍໍາຂອງແສງເລເຊີອະນຸຍາດໃຫ້ສໍາລັບການຮັງແຫນ້ນຂອງພາກສ່ວນ, ການເພີ່ມປະສິດທິພາບການນໍາໃຊ້ແຜ່ນໂລຫະແລະຫຼຸດຜ່ອນການຂູດ. ນອກຈາກນັ້ນ, ຂອບທີ່ສະອາດ, ບໍ່ມີ burr ທີ່ຜະລິດໂດຍການຕັດ laser ມັກຈະລົບລ້າງຄວາມຕ້ອງການສໍາລັບການ deburring ຫຼືສໍາເລັດຮູບຕື່ມອີກ, ປັບປຸງຂະບວນການຜະລິດແລະຫຼຸດຜ່ອນເວລາແລະຄ່າໃຊ້ຈ່າຍໃນການຜະລິດໂດຍລວມ.
versatility ຂອງການຕັດ laser ຂະຫຍາຍເກີນຄວາມແມ່ນຍໍາແລະປະສິດທິພາບ. ດ້ວຍຄວາມສາມາດໃນການຕັດໂລຫະທີ່ຫລາກຫລາຍ, ລວມທັງເຫຼັກກ້າ, ອາລູມິນຽມ, ແລະສະແຕນເລດ, ເຊັ່ນດຽວກັນກັບວັດສະດຸທີ່ບໍ່ແມ່ນໂລຫະເຊັ່ນ: ພາດສະຕິກແລະອົງປະກອບ, ການຕັດດ້ວຍເລເຊີໄດ້ສະຫນອງການນໍາໃຊ້ຢ່າງກວ້າງຂວາງ. ຈາກກະດານສະຖາປັດຕະຍະກໍາແລະປ້າຍໄປຫາເຄື່ອງປະດັບທີ່ສັບສົນແລະຊິ້ນສ່ວນລົດຍົນທີ່ກໍາຫນົດເອງ, ຄວາມເປັນໄປໄດ້ສໍາລັບໂລຫະແຜ່ນ laser ຕັດແມ່ນເກືອບບໍ່ຈໍາກັດ.
ນອກເຫນືອຈາກຄວາມແມ່ນຍໍາແລະຄວາມຄ່ອງແຄ້ວຂອງມັນ, ການຕັດເລເຊີຍັງສະຫນອງປະໂຫຍດຂອງອັດຕະໂນມັດແລະການເຊື່ອມໂຍງກັບການອອກແບບຄອມພິວເຕີ (CAD). ໂດຍການນໍາໃຊ້ຊອບແວກ້າວຫນ້າທາງດ້ານແລະການຂຽນໂປລແກລມ CNC, ການອອກແບບແລະຮູບແບບທີ່ສັບສົນສາມາດແປເປັນເສັ້ນທາງຕັດທີ່ຊັດເຈນດ້ວຍຄວາມສະດວກສະບາຍ. ການປະສົມປະສານຂອງການອອກແບບແລະການຜະລິດແບບບໍ່ມີ seamless ນີ້ອະນຸຍາດໃຫ້ສໍາລັບ prototyping ຢ່າງໄວວາແລະການປັບຕົວໄວເພື່ອການປ່ຽນແປງການອອກແບບ, ເຮັດໃຫ້ການຕັດ laser ເປັນການແກ້ໄຂທີ່ເຫມາະສົມສໍາລັບການທັງສອງໂຄງການ custom ຂະຫນາດນ້ອຍແລະການຜະລິດຂະຫນາດໃຫຍ່ແລ່ນ.
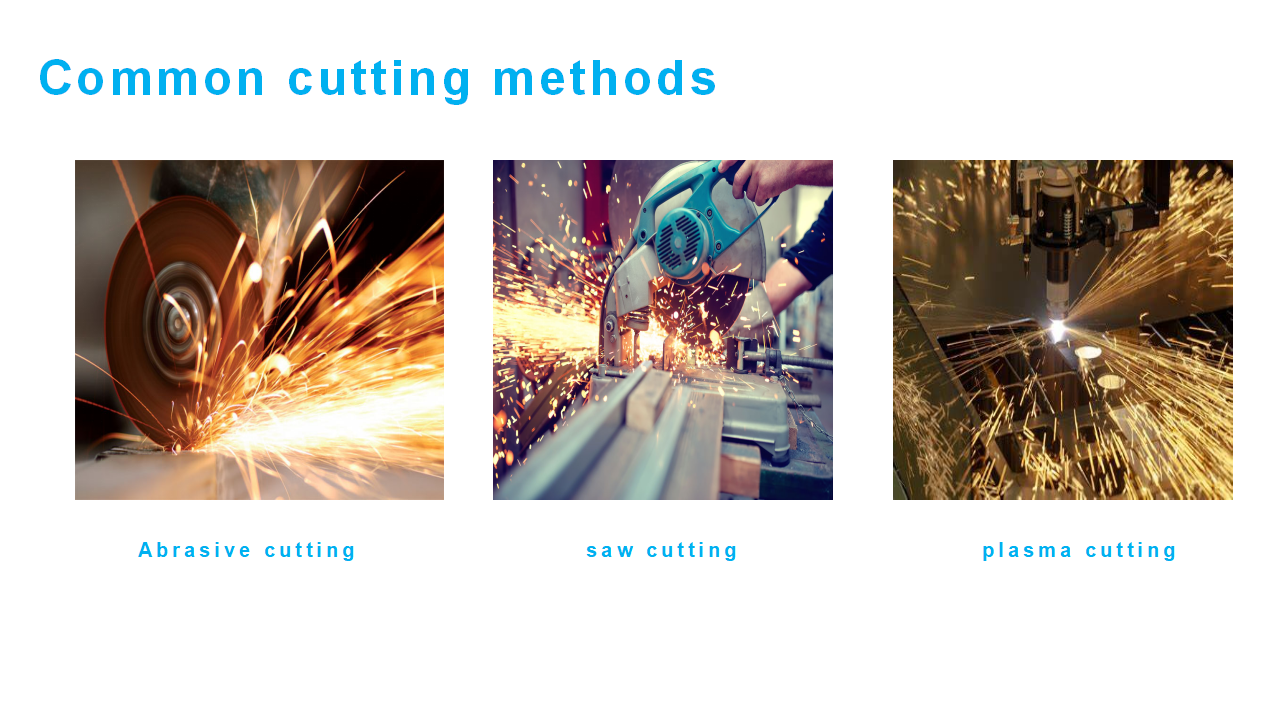
ໃນຂະນະທີ່ການຕັດດ້ວຍເລເຊີໄດ້ຫັນປ່ຽນໂລກຂອງການຜະລິດແຜ່ນໂລຫະຢ່າງບໍ່ຕ້ອງສົງໃສ, ມັນເປັນສິ່ງສໍາຄັນທີ່ຈະສັງເກດວ່າເຕັກໂນໂລຢີທີ່ກ້າວຫນ້ານີ້ຕ້ອງການຄວາມຊໍານານແລະການພິຈາລະນາຢ່າງລະມັດລະວັງ. ປັດໃຈເຊັ່ນ: ຄວາມຫນາຂອງວັດສະດຸ, ພະລັງງານເລເຊີ, ຄວາມໄວການຕັດ, ແລະທາດອາຍແກັສການຊ່ວຍເຫຼືອທັງຫມົດມີບົດບາດສໍາຄັນໃນການບັນລຸຜົນໄດ້ຮັບທີ່ດີທີ່ສຸດ. ນອກຈາກນັ້ນ, ການບໍາລຸງຮັກສາທີ່ເຫມາະສົມແລະການປັບຕົວຂອງອຸປະກອນການຕັດ laser ເປັນສິ່ງຈໍາເປັນເພື່ອຮັບປະກັນການຕັດທີ່ສອດຄ່ອງ, ທີ່ມີຄຸນນະພາບສູງ.
ສະຫລຸບລວມແລ້ວ, ສິລະປະຂອງການຕັດໂລຫະທີ່ມີຄວາມແມ່ນຍໍາໄດ້ບັນລຸຄວາມສູງໃຫມ່ດ້ວຍການມາຮອດຂອງເຕັກໂນໂລຊີການຕັດ laser. ດ້ວຍຄວາມແມ່ນຍໍາ, ປະສິດທິພາບ, ຄວາມຄ່ອງແຄ້ວ, ແລະການເຊື່ອມໂຍງກັບການອອກແບບທີ່ທັນສະໄຫມແລະຂະບວນການຜະລິດ, ການຕັດ laser ໄດ້ກາຍເປັນພື້ນຖານຂອງອຸດສາຫະກໍາການຜະລິດໂລຫະແຜ່ນ. ໃນຂະນະທີ່ຄວາມຕ້ອງການຂອງອົງປະກອບໂລຫະທີ່ສັບສົນ, ຄຸນນະພາບສູງຍັງສືບຕໍ່ຂະຫຍາຍຕົວໃນທົ່ວອຸດສາຫະກໍາຕ່າງໆ, ການຕັດ laser ຢືນເປັນຫຼັກຖານສະແດງເຖິງສິລະປະແລະນະວັດກໍາທີ່ຊຸກຍູ້ວິວັດທະນາຂອງການເຮັດວຽກໂລຫະ.
ບໍ່ວ່າຈະເປັນການສ້າງລັກສະນະສະຖາປັດຕະຍະກໍາທີ່ຊັບຊ້ອນ, ອົງປະກອບທີ່ຊັດເຈນສໍາລັບການນໍາໃຊ້ໃນອາວະກາດ, ຫຼືສິນລະປະໂລຫະທີ່ກໍາຫນົດເອງ, ສິນລະປະຂອງການຕັດໂລຫະທີ່ມີຄວາມແມ່ນຍໍາໂດຍຜ່ານເຕັກໂນໂລຊີ laser ຍັງສືບຕໍ່ຊຸກຍູ້ຂອບເຂດຂອງສິ່ງທີ່ເປັນໄປໄດ້ໃນໂລກຂອງ fabrication ໂລຫະແຜ່ນ. ໃນຂະນະທີ່ເຕັກໂນໂລຢີສືບຕໍ່ກ້າວຫນ້າ, ມັນຫນ້າຕື່ນເຕັ້ນທີ່ຈະຈິນຕະນາການຊາຍແດນໃຫມ່ທີ່ການຕັດດ້ວຍເລເຊີຈະສືບຕໍ່ຄົ້ນຫາ, ການສ້າງອະນາຄົດຂອງການເຮັດວຽກໂລຫະທີ່ມີຄວາມແມ່ນຍໍາແລະຄວາມຄິດສ້າງສັນທີ່ບໍ່ມີຕົວຕົນ.
ຕິດຕໍ່ພວກເຮົາສໍາລັບຂໍ້ມູນເພີ່ມເຕີມ
ອີເມວ:chinaroyalsteel@163.com
ໂທ/WhatsApp: +86 15320016383
ເວລາປະກາດ: 21-05-2024